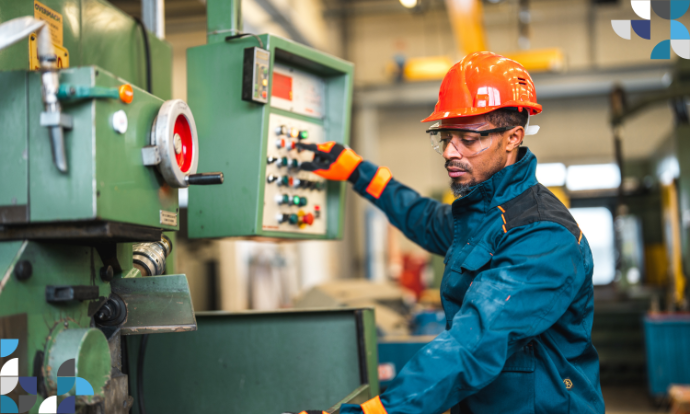
In today’s digitally driven world, organizations depend on technology more than ever—making them increasingly exposed to cyber threats.
Across our blogs, we regularly explore emerging cyber risks, the tools and strategies available to mitigate them, compliance considerations, and real-world customer stories that illustrate both challenges and solutions.
While this information is critical, it typically centers on IT infrastructure. Yet, many organizations also rely on operational technology (OT)—often the core of their production and service delivery. For these businesses, OT security is not optional; it’s essential. It’s time to bring OT into the cybersecurity conversation.
IT
Every organization relies on IT, which supports the management and security of critical functions such as email, financial transactions, human resources (HR), and a wide range of applications hosted in data centers and the cloud.
IT primarily focuses on the information-facing activities of a business. The IT department is responsible for managing the company’s information infrastructure—ensuring the security of sensitive applications and confidential data, as well as maintaining data availability. This infrastructure includes various devices, such as servers and workstations, and the networks that connect them.
OT
Operational Technology (OT) refers to the systems used to connect, monitor, manage, and secure an organization’s industrial activities. Companies involved in manufacturing, mining, utilities, logistics, and similar sectors often depend far more on OT than those delivering purely digital or service-based offerings.
Examples of OT include robots, industrial control systems (ICS), programmable logic controllers (PLCs), and many other specialized systems.
OT is commonly found in production environments and factory floors, but it also plays a role in public spaces—such as parking meters, ATMs, electric vehicle charging stations, and more. While IT is focused on front-end information systems, OT supports back-end operations: machines, production equipment, and Internet of Things (IoT) devices.
The OT department is responsible for industrial equipment and infrastructure at operational sites. Their focus is on output—the results of the production chain—and the safety of employees. In these environments, uptime is critical. A system failure can halt entire business processes, leading to immediate and significant financial losses.
In addition, machines often generate valuable data that must be stored and analyzed to monitor industrial processes. This data supports informed decision-making, enabling predictive maintenance and more efficient operations.
Typical IT and OT devices
IT devices are generally easy to maintain, readily replaceable, and run on widely used operating systems such as Windows, iOS, or Linux. Your laptop is a perfect example.
In contrast, OT devices are typically purpose-built to perform a single, specialized function. They operate with dedicated software tailored to that task and are designed for long-term use—often lasting decades. Because they manage critical infrastructure, uninterrupted operation is a top priority.
However, OT systems often come with inherent challenges. They may have numerous software vulnerabilities, and their access and management can be complex and sensitive. Even minor changes—such as a routine software update—can have serious implications for operational processes. OT assets encompass a wide range of equipment, including filling or injection machines, pumps, packaging systems, distribution networks, wind turbines, EV chargers, and ticketing kiosks.
How do OT and IT Networks differ?
While OT and IT network infrastructures share some common components—such as switches, routers, and wireless technologies—their design, purpose, and operating environments differ significantly. Network management and security practices developed for IT have certainly proven beneficial in OT environments as well.
However, several key distinctions remain:
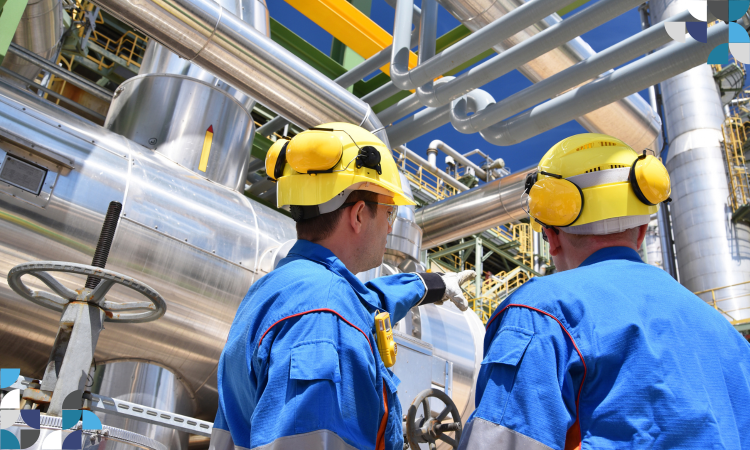
- Form Factor & Flexibility: OT network devices are typically smaller and modular in
design, allowing them to be mounted in a variety of ways—on rails, walls, light poles, inside
vehicles, or embedded within other machinery.
- Durability: OT infrastructure is built to endure harsh industrial environments. It must
withstand shock, vibration, moisture, extreme temperatures, corrosive air, and exposure to
chemicals—conditions rarely encountered in traditional IT settings.
- Connectivity & Protocols: OT network devices interconnect IoT sensors and machinery
and must support a wide range of communication protocols. These can include industrial
and wireless protocols specific to their use case.
- Specialized Networks: Depending on their application, OT devices may use networks such as LoRaWAN, Sigfox, RPMA, Weightless, NB-IoT, or Wi-SUN to support industrial IoT (IIoT) connectivity. In contrast, IT systems typically rely on standard interfaces like LAN, PAN, WAN, and VPN.
Understanding concrete Cyber Threats in OT
Wondering what kinds of cyber threats could impact your OT environment? Here are a few real- world scenarios:
- Unplanned Downtime: A cyberattack targeting your OT network shuts down production
unexpectedly. Considering that the average downtime after a ransomware attack in
manufacturing is 11.6 days, the resulting financial and operational damage can be severe.
- Manipulated Machine Settings: Hackers alter machine parameters, leading to defective
products or damaged equipment. This can trigger industrial accidents, cause injury, expose
your organization to legal liabilities, and endanger both employees and end-users.
- Data Theft and Espionage: Your operational data or trade secrets are stolen during a breach and sold to competitors. The result? Loss of competitive edge, reputational harm, and long- term business impact.
Read our next blog what you need to take into account to increase your OT security.
OT-Security vs IT-Security